Process
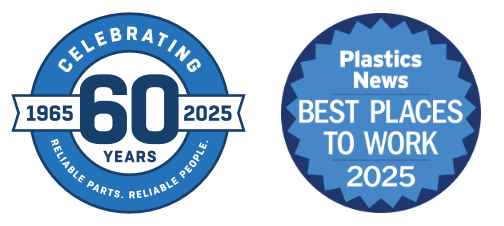
Reliable parts are the result of reliable people following a reliable process.
You matter.
What differentiates Steinwall from its competitors more than anything is not the type of machinery we have or the type of parts we make, it’s the experience of how our customers are treated throughout the entire process, regardless of the product. Steinwall has been diligently refining every step in the plastic injection molding process to ensure reliable manufacturing of quality parts that exceed our customers’ expectations. Our process innovations have been recognized by both our customers and by our peers in the plastic injection molding industry.
01 Design
Steinwall has one of the most educated design and engineering teams in the industry, giving your product a leading edge from the very beginning. We are accustomed to working with our customers’ engineering teams early in the process to develop a part design that will meet all specifications and be efficiently manufactured by plastic injection molding. Our knowledge and experience enables us to recommend the best resins, part geometry and press equipment for the producing the most reliable and economical parts to fit our customer’s application.
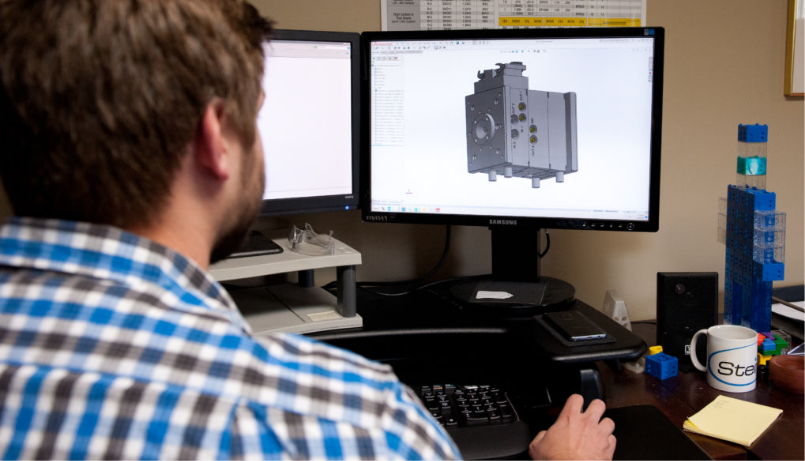
02 Engineer
Our engineering services help customers refine the project’s plan and concept for efficiency during prototype development. Using state-of-the-art 3D CAD image rendering, we optimize the design for manufacturability and provide a first visual look at your concept. Prototype parts and tools can be 3D printed using various materials for testing and proof of concept.
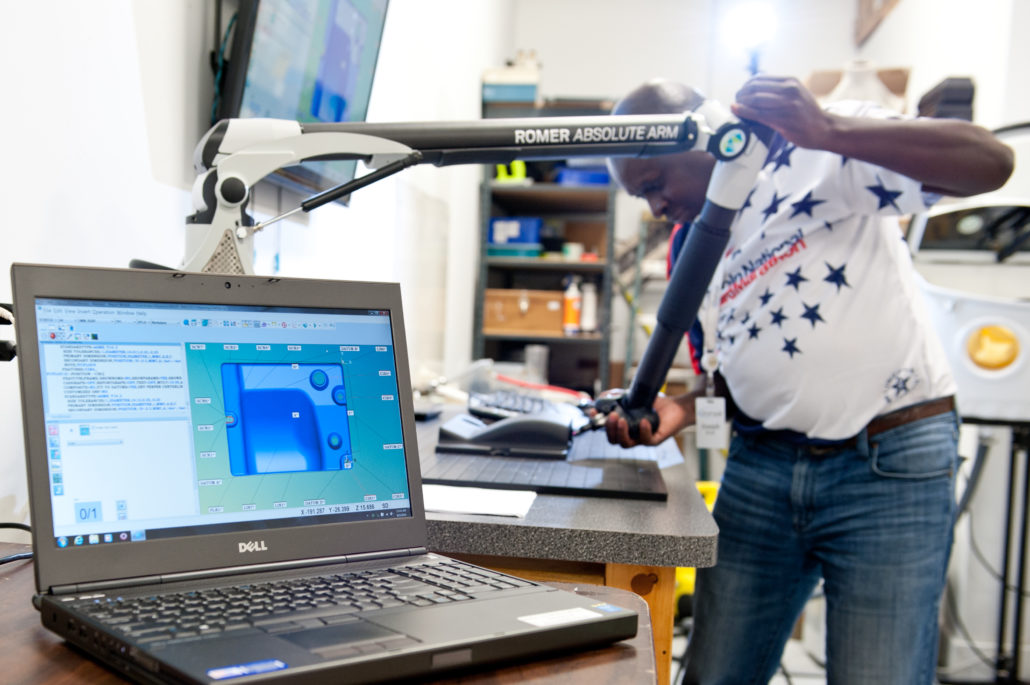
03 Mold
Tooling the mold requires extraordinary accuracy and craftsmanship. Preparing a precise tool that efficiently produces a high quality part is an important investment and is critical to producing reliable parts over the lifetime of the project. Steinwall began as a mold making shop in 1965 and has more than a half-century history of developing plastic injection molding tools for manufacturing high quality plastic parts.
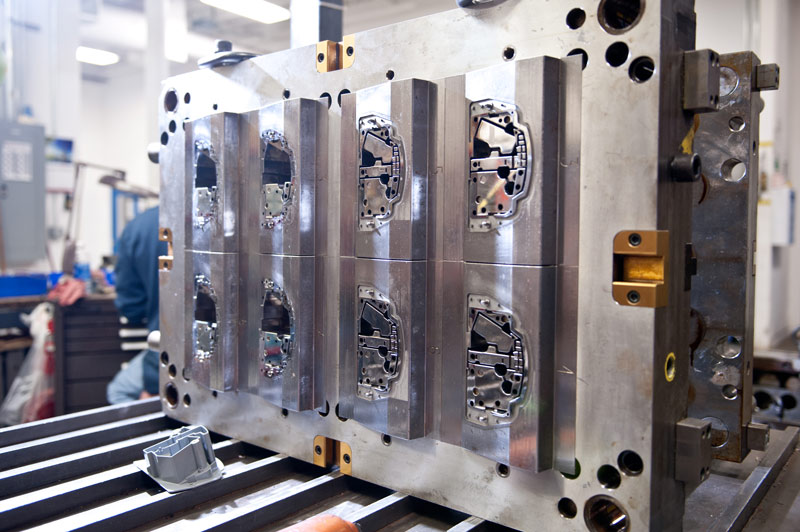
04 Manufacture
Steinwall’s incredibly diligent and experienced production team is equipped with today’s top of the line plastic injection molding equipment and technology. Adhering to the highest quality standards, every project and prototype is manufactured by our highly educated team. Our processes are carefully engineered to match the unique requirements of each product and material to produce the most efficient and reliable finished parts. Steinwall also performs onsite assembly and secondary operations to provide customers with a completed part, ready for their lean manufacturing processes. From product ornamentation and high-speed automated assembly, to hand-checked product assembly, this important step in the production process is treated with utmost care. Finishing services can include: Drilling, Taping, Sonic Welding, Hot Stamping, Packaging, Pad Printing and more.
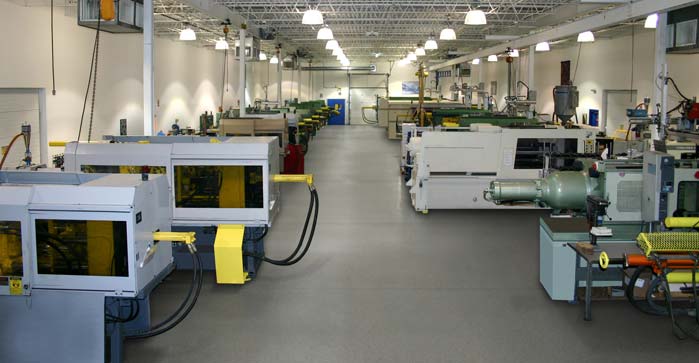
05 Analyze
Steinwall production teams operate under strict quality management processes. Not only are parts carefully measured to meet customer specifications, every project is carefully monitored for cost effectiveness, budget tracking, product reliability, on-time delivery, and total customer satisfaction. We are constantly looking for ways to give our customers more value.
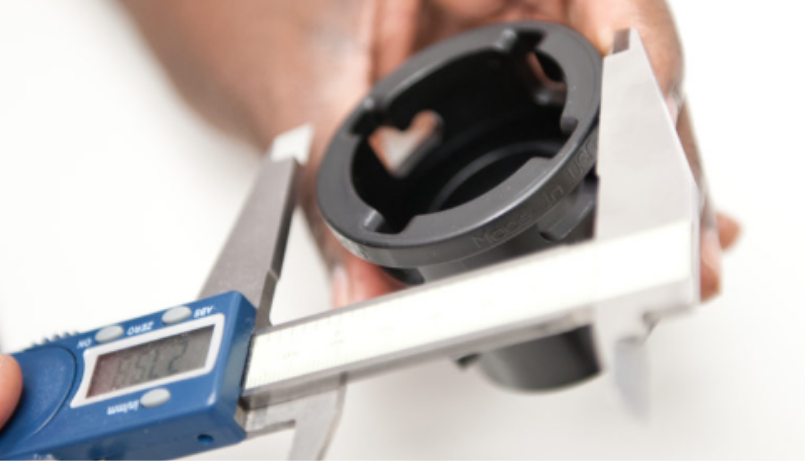
06 Warehouse
Manufacturing reliable plastic injection molded parts is not enough to meet the needs of our customers who operate lean manufacturing environments. Just In Time supply chain management is critical to maintaining efficient production and reliable suppliers are essential. Steinwall is devoted to providing flawless North American distribution services to help customers exceed their lean manufacturing goals. We are proud of our 99.99% on-time delivery. Our inventory management and delivery solutions complete the project with a variety of system options including EDI or Web Order Management, Blanket Product Orders, Just In Time Systems, Returnable Containers, Warehouse Storage, and eKanban.
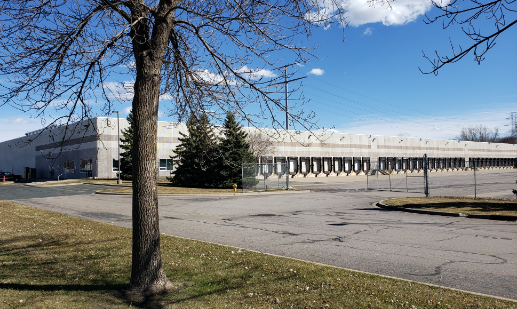
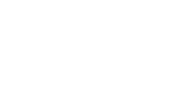
763.767.7060
1.800.229.9199
1759 116th Avenue
Minneapolis, MN 55448
Follow Us
Services
Company